Corrosion Comparison of Metals in Dynalene HC and CaCl2 Brine
Dynalene HC is a potassium formate and water based heat transfer fluid used in several low temperature applications. Dynalene HC is a non-toxic, non-flammable, environmentally friendly fluid which demonstrates higher thermal efficiency, lower viscosity and lower corrosion rate as compared to other brines (e.g. CaCl2). Presence of chloride in the fluid causes several forms of corrosion including localized, pitting and stress-corrosion cracking. Dynalene HC with an ideal pH and premium corrosion package protects the metals and the fluid from any degradation. Dynalene performed several corrosion tests over the years with our HC series of fluids and compared the results with CaCl2 and other water based heat transfer fluids.
New Product Watch
Dynalene MT high temperature heat transfer fluid
Dynalene is proud to announce the launch our newest high temperature heat transfer fluid Dynalene MT. Dynalene MT is a safe and non-toxic fluid with an operating temperature range of 32°F to 662°F / 0°C to 350°C. This fluid offers exceptional thermal stability as well as a low vapor pressure and a high boiling point throughout its temperature range. Dynalene MT is competitively priced in applications including open baths, extrusion/injection molding and many other closed loop systems. For more information about this product please click here. Pitting Corrosion is very important in metals in the presence of chloride and other aggressive types of anions. Dynalene performed electrochemical testing, like Cyclic Polarization, which helped in determining the pitting tendency and its ability to form a passivating layer on a metal surface. Both Carbon Steel and Copper, after 4 days of immersion in the coolants, demonstrated very high resistance to pitting and more than 100 times lower corrosion rate in Dynalene HC as compared to CaCl2 brine. The Cyclic Polarization experiment showed that the inhibitor package in HC-40 inhibits metals like copper and carbon steel and provides superior corrosion resistance compared to CaCl2 fluid.
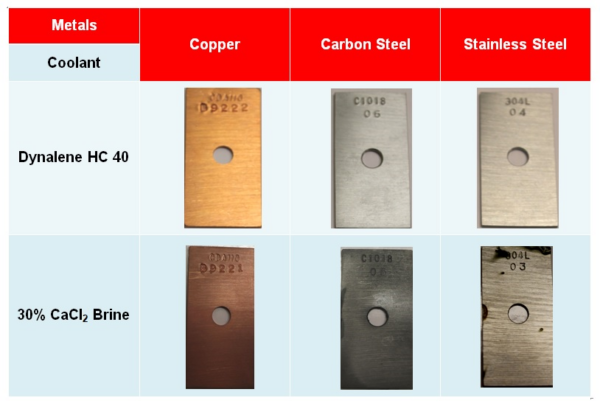
Experiments conducted by Dynalene showed that Copper, Carbon Steel and Stainless Steel are all very compatible with HC-40 while these metals showed significant signs of general and pitting corrosion in the Calcium Chloride solution.
Dynalene also tested the compatibility of carbon steel, stainless steel and copper at 80°C for 250 hrs in Dynalene HC and CaCl2. The CaCl2 brine solution in contact with the steel and copper samples turned yellowish brown and bluish in color, respectively. It was observed that loose corrosion debris formed on the metal surfaces contaminated the Calcium Chloride coolant. The Dynalene HC fluid was completely clear after the immersion testing. The metal samples in contact with CaCl2 brine solution also showed discoloration, corrosion product build-up, but the samples were clean with no signs of corrosion in presence of the Dynalene HC
Choosing a Coolant and Materials for PEM Fuel Cells
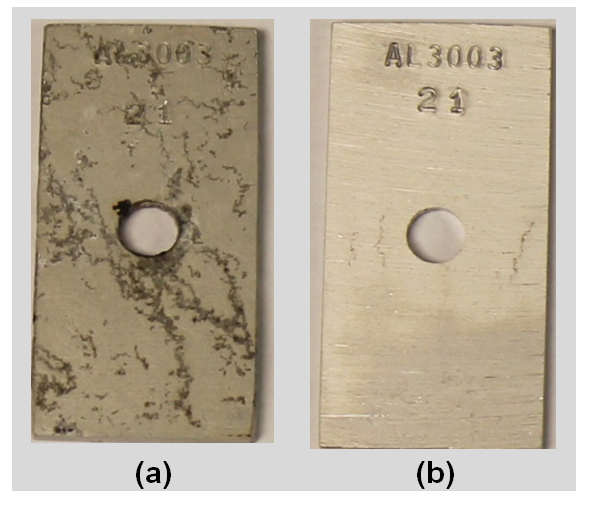
An important aspect of PEM fuel cell design is the understanding of the coolants and materials of construction of the cooling loop. The coolant must be efficient and the materials cannot degrade and add ions into the fluid. The combination should achieve a low electrical conductivity (less than 10 μS/cm) or the system could short or cause hydrolysis of the electrolyte.
In most liquid cooled PEM fuel cells, deionized (DI) water or DI water/uninhibited glycol mixtures are used because of their initial low electrical conductivity and the ability to use a DI filter, which maintains a low electrical conductivity in the coolant. DI water and DI water/uninhibited glycol mixtures are good solutions for liquid cooling because of their thermo-physical properties, but do not protect against corrosion because neither has an inhibitor package. Typical inhibitor packages cannot be added to coolants because they greatly increase the electrical conductivity due to their ionic nature and DI filters cannot be used for the same reason.
Dynalene has two fluids, Dynalene FC and Dynalene LC, to reduce corrosion and maintain low electrical conductivity that were created with PEM fuel cells in mind. Each fluid is water based and uses a non-ionic corrosion inhibitor package. This inhibitor package is the same for both coolants and does not affect the DI filters in the system. The main difference between the two coolants is Dynalene FC does not need a DI filter to remove ions from the fluid. Dynalene FC contains ion scavenging nanoparticles that help in deionization of the fluid.
Material selection is also important in preventing an increase in electrical conductivity or fouling the radiators in the system. Dynalene has experimented with a number of materials in various coolants to find the best combinations. The coolants selected were DI water, DI water/uninhibited glycol mixtures, Dynalene FC, and Dynalene LC. Typical materials of construction were submersed in the coolants for 5000 hours and the temperature was maintained at 80°C. The results showed that most of the metals and polymers had intermediate to severe degradation in DI water and DI water/uninhibited glycol mixtures. Degradation was measured using three methods, change in pH, electrical conductivity and surface analysis of the material. The Dynalene FC and the Dynalene LC showed only small changes in these areas. Dynalene would recommend using Aluminum, Brass, Copper and Stainless Steel as the metals while Silicone, Polypropylene, HDPE, LDPE and Tygon should be the polymers chosen.
For more complete list of materials or if you have any questions please contact Dynalene by phone 1.877.244.5525 or by email info@dynalene.com.