Glycol Regeneration
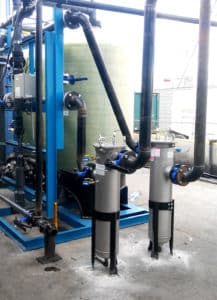
Dynalene offers contamination removal systems that can remove both particulate and ionic contaminants in glycol-based heat transfer fluids. These systems can be used in a slipstream or in the main loop for continuous contamination removal without having to stop the existing process. Dynalene’s systems can remove ionic contaminations such as chloride, molybdate, calcium, magnesium, sulfate, acetate, selenium, arsenic, and more.
Dynalene’s chloride removal system can be used in a variety of applications, such as natural gas storage and extraction, cooling loops in power plants, and applications where heat transfer fluid is contaminated with an ionic compound (i.e. salts). High chloride concentration in heat transfer fluid can cause corrosion, system clogging with salts, reduction in heat transfer efficiency and can sometimes lead to system shutdowns. Our system helps to maintain a very low chloride level while the existing process is still in operation, so that
costly shutdowns and maintenance are avoided.
Dynalene’s comprehensive filtration solutions are compatible with most heat transfer fluids. The filtration products are available in various sizes, each with customization options like materials of construction, fluid handling capacity, and flow rate. These filters are designed and tested to be used with glycol based fluids like propylene glycol, ethylene glycol, and triethylene glycol, and can be custom built for any application. Click here to know more about our filtration products.
Glycol-based heat transfer fluid can become fouled for various reasons after circulating in a system for a long time. Contamination issues can be caused due to particulates or ionic contaminants that are dissolved in the glycol-water mixture. Some common issues that are seen in glycol-based systems are:
- Particulate contamination turns the fluid a darker color and may result in a decrease in heat transfer efficiency.
- Foaming in the heat transfer fluid creates false readings in gauges and sensors.
- Pipe blockage issues due to corrosion and erosion, which may be caused by corrosive ionic contaminants and particulate contaminants respectively.
- Rust buildup issues in the pumps due to the presence of corrosion debris in the fluid.
- Presence of metal shavings and solder particles from when the system was built.
Due to our in-house laboratory capabilities and our extensive experience with heat transfer fluids, we can test the fluid samples to determine the amount of contaminants and the effect that they may have on your system. Contact us today at 610.262.9686 or email at info@dynalene.com and let us help you determine the best contamination removal product that will work for your application. Additionally, we also offer basic testing devices that can be used for fluid property measurements in order to monitor the health of your fluids.